Five important reasons why you should digitalise the flow of information in production right now
Author: Lauri Antalainen
When implementing production, it is important to consider how work orders are transmitted to production and how the implementation of these work orders is reported. The organisation of production management can be judged by its digitalisation:
- At one end of the scale, production will be completely paperless, with work orders, their reporting, stocking and other operations fully digitalised and in real time.
- At the other end of the scale is the type of manufacturing, where work orders, drawings and other information are printed out in the office, taken to the production floor, where these papers then make their ‘rounds’ and come back to the office with notes made by the production worker. In the office, someone collects these papers and enters the information, usually either into an accounting program or Excel.
Non-digital, paper-based production management has a number of other important shortcomings that can be eliminated through digitalisation, in addition to the miles-long daily transportation of documents by workers.
Five important reasons why you should digitalise the flow of information in production right now are:
1. Post-calculation and cost price calculation
Post-calculation should be an integral part of the core process of any manufacturing company. Unfortunately, many companies still do not do this (or do it only partially) because they lack the information needed to carry out post-calculation. This, in turn, means that the calculation of cost price of the product and of production itself (cost estimate) on which the quotations are based is often inaccurate and the prices offered to customers are sometimes too high and sometimes too low. Even more problematic is the fact that a company tends to win bids that are too low, more often than average, while it loses work to competitors with bids that have been made too high. The result is lower profitability and lost work.
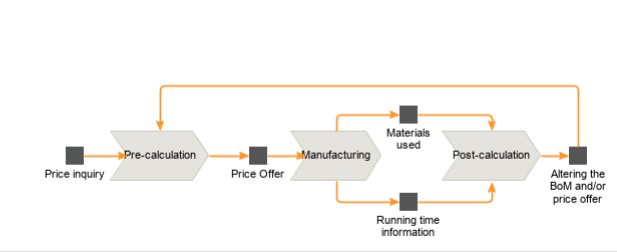
To perform a post-calculation, the following digital information is needed: the amount of material actually used to manufacture the product and the time spent on operations. The collection of information requires work reporting on a work centre basis and the existence of a system of stock records related to production orders. Only a digitalised process can ensure sufficiently accurate accounting of both material and time consumption.
2. Tracking and partial reporting of production orders
A major problem in non-digitised production management is the lack of information in the office about the status of one or another production order currently in production. It is not possible to respond to a customer’s queries about the delivery time of a product without asking for this information on the production floor. Even more problematic is the situation where, for one reason or another, it is not possible to complete a production order, but there is a wish to invoice (and potentially ship to the customer) the items or quantities already produced. Partially reporting the completion of work orders on paper is complex and requires a lot of non-value-added activities both in production and in the office.
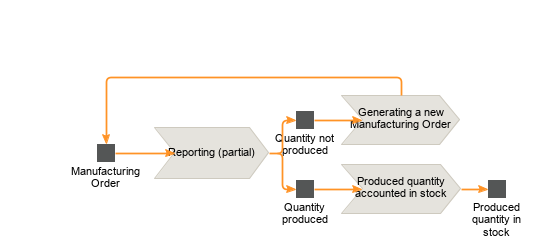
In order to digitalise partial reporting of production orders, MRP functionality should be available in the work centre to allow partial reporting of a production order, ideally automatically generating a new work order for the unreported part.
3. Monitoring OEE – Overall Equipment Effectiveness – and occupancy of work centres
The importance of monitoring the occupancy of work centres has been recognised for many years, and a number of production facilities, also otherwise poorly digitalised ones, have introduced external tools to measure and visualise overall equipment effectiveness and cycle times. While useful, there are also problems with using such external tools (especially if they are not linked to the company’s ERP system) – describing the nuances of deviations from the norm/cycle times is often an extra task that production workers do not have the time or the work ethic for, and is often left undone. The result is knowing that overall equipment effectiveness was low, without knowing what caused it and what could be done to prevent it in the future.
Fully digitalised production order transmission and reporting, and the digital, real-time handling of additional information – workers on the shop floor, job types, etc. – will take overall equipment effectiveness monitoring and the related analytics to a qualitatively new level. A decrease in overall equipment effectiveness can be immediately linked to various parameters such as the worker, the type of production order and its parameters, the raw materials used, etc. In addition to the knowledge that the overall equipment effectiveness is at level X, knowledge of the associated circumstances is also added. In well-digitalised production, the company’s own information system is often sufficient to monitor overall equipment effectiveness, and no external tools are needed.
4. Information and analysis of non-conformities
The monitoring of non-conformities (or defects) and the gathering of information on them is already carried out by the vast majority of manufacturing companies operating in Estonia. If what is happening on the production floor has not been digitalised, the typical solution is a sheet of paper with a predefined description of the non-conformity and the likely cause. These sheets of paper are collected, the information on them is entered into Excel, and a meeting is held once a week or month to analyse the information on such non-conformities.
Collecting this kind of information is certainly helpful, but nowhere near as effective as digitally collecting the information on non-conformities in a structured and digitally processable form. While the analysis of non-conformities in Excel usually focuses on the most recent acute cases, structured nonconformity information, linked to predefined defect codes and specific orders, allows one to keep an eye on the ‘bigger picture’ and to see correlations between the occurrence of a non-conformity and the work centre/worker/technology/type of work and other parameters. Only having digital and structural information enables one to take data-driven management decisions to further prevent non-conformities.
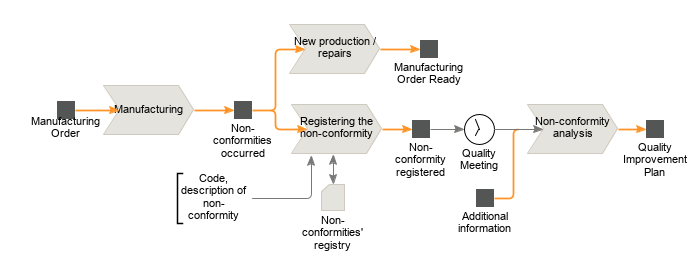
5. BI – Business Intelligence
Last but not least, a very important reason to digitalise what happens on the shop floor is the capacity that will be created to implement different types of business intelligence. The management of what is happening on the shop floor, in the form of work order transmission and reporting, generates a wealth of operational information that is of much higher quality (more accurate and comprehensive) than that collected manually and stored in Excel. Operational information gathered in this way on a day-to-day basis can later be used to make or support different types of business decisions, whether related to investment, human resources, production management, etc.
The article originally appeared in two parts in Äripäev’s thematic news site Tööstusuudised:
Info liikumise digitaliseerimise 2 põhjust tootmises: järelkalkulatsioon ja osaline raporteerimine – Tööstusuudised (toostusuudised.ee)